Discover What is Porosity in Welding and Its Impact on Structural Honesty
The Science Behind Porosity: A Comprehensive Overview for Welders and Fabricators
Understanding the detailed systems behind porosity in welding is important for welders and fabricators aiming for flawless craftsmanship. From the structure of the base products to the intricacies of the welding procedure itself, a multitude of variables conspire to either exacerbate or ease the existence of porosity.
Understanding Porosity in Welding
FIRST SENTENCE:
Evaluation of porosity in welding reveals vital understandings right into the integrity and top quality of the weld joint. Porosity, defined by the presence of dental caries or voids within the weld steel, is a typical concern in welding processes. These voids, otherwise properly attended to, can jeopardize the structural integrity and mechanical buildings of the weld, resulting in prospective failings in the finished product.
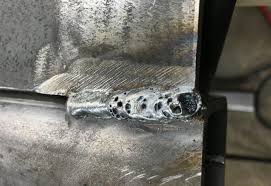
To spot and measure porosity, non-destructive screening methods such as ultrasonic screening or X-ray evaluation are usually used. These techniques permit for the recognition of interior defects without compromising the integrity of the weld. By evaluating the size, form, and distribution of porosity within a weld, welders can make informed decisions to boost their welding processes and accomplish sounder weld joints.
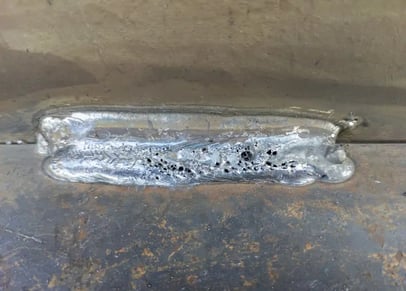
Elements Influencing Porosity Development
The occurrence of porosity in welding is affected by a myriad of variables, varying from gas protecting efficiency to the ins and outs of welding parameter settings. Welding specifications, including voltage, current, take a trip speed, and electrode kind, also influence porosity development. The welding method employed, such as gas steel arc welding (GMAW) or secured metal arc welding (SMAW), can influence porosity formation due to variations in warmth distribution and gas protection - What is Porosity.
Effects of Porosity on Weld High Quality
Porosity formation considerably jeopardizes the architectural stability and mechanical properties of bonded joints. When porosity exists in a weld, it creates spaces or cavities within the material, decreasing the overall toughness of the joint. These spaces function as stress and anxiety concentration factors, making the weld a lot more susceptible to splitting and failure under lots. The visibility of porosity also damages the weld's resistance to corrosion, as the entraped air or gases within the voids can react with the surrounding atmosphere, bring about degradation gradually. In addition, porosity can prevent the weld's ability to stand Our site up to stress or impact, more jeopardizing the overall quality and reliability of the bonded framework. In vital applications such as aerospace, auto, or structural buildings, where safety and sturdiness are paramount, the harmful results of porosity on weld quality can have severe repercussions, emphasizing the relevance of lessening porosity with proper welding techniques and procedures.
Techniques to Decrease Porosity
To improve the quality of welded joints and ensure architectural honesty, welders and makers use details methods focused on decreasing the development of spaces and dental caries within the material throughout the welding process. One effective technique to reduce porosity is to make sure proper material prep work. This includes extensive cleansing of the base steel to eliminate any type of contaminants such as oil, grease, or wetness that might contribute to porosity development. Furthermore, making use of the proper welding criteria, such as the right voltage, present, and travel speed, is vital in preventing porosity. Keeping a regular arc length and angle during welding additionally helps in reducing the chance of porosity.

Making use of the ideal welding technique, such as back-stepping or employing a weaving motion, can additionally help distribute warm equally and decrease the chances of porosity development. By implementing these techniques, welders can efficiently decrease porosity and produce top quality bonded joints.

Advanced Solutions for Porosity Control
Implementing innovative technologies and ingenious approaches plays a pivotal duty in accomplishing exceptional control over porosity in welding processes. Additionally, utilizing advanced welding strategies such as pulsed MIG welding or customized atmosphere welding can also help reduce porosity problems.
An additional advanced service involves using innovative welding devices. As an example, using devices with integrated features like waveform control and advanced power sources can enhance weld top quality and reduce porosity threats. Furthermore, the application of automated welding systems with accurate control over criteria can substantially minimize porosity defects.
In addition, including innovative tracking and inspection modern technologies such as real-time X-ray imaging or automated ultrasonic testing can assist in spotting porosity early in the welding process, enabling prompt rehabilitative actions. Overall, incorporating these advanced options can significantly boost porosity control and enhance the overall quality of bonded components.
Verdict
In verdict, understanding the science special info behind porosity in welding is vital for welders and fabricators to generate top notch welds - What is Porosity. Advanced options for porosity control can better enhance look at more info the welding procedure and make certain a strong and reliable weld.